It’s never too late to get involved in workplace health and safety (WHS). At CTF, we understand the importance of fostering safe and healthy workspaces. We know how exciting and dynamic construction workplaces can be–but also their dangers. By learning about safe work practices, we can develop inviting, hazard-free workplaces for ourselves and others. That’s why we’ve created a handy guide on workplace safety in construction, including all the tips and tricks to keeping yourself, and your workmates, safe all year round.
Who is responsible for workplace safety?
Safety is everyone’s responsibility. Although your employer or main contractor is at the forefront of implementing health and safety guidelines, look out for yourself and your workmates. Work health and safety advisors also lead the charge in developing and implementing safe workplace procedures and plans.
Employer or main contractor
Employers or main contractors are your first point of call when it comes to workplace safety. Conducting regular safety inspections, ensuring staff are properly trained, and providing safe equipment are all an employer’s responsibility. They should also create an environment where staff feel safe talking to them about potential workplace hazards.
As an employer, it’s up to you to periodically review the structure and operation of your workplace, identify areas of concern, and implement plans to rectify harmful behaviour or situations.
Workers
Construction work in and out of the office can be tricky, so it’s important to consider yourself and your workmates when completing tasks. Something as simple as wearing the right protection, observing safety signs, or keeping an eye on your surroundings can prevent accidents and injury.
WHS advisors
Work health and safety advisors identify and investigate workplace hazards. Got a safety issue? They’re on the case! WHS advisors, or officers, educate others about workplace safety. They might be brought on to perform risk assessments on a project, inspect a workplace or construction site, or deliver training to staff and employers.
In some cases, WHS advisors are needed after an accident has occurred so they can observe the accident site and understand how it could have been prevented. This information is used to create better and more comprehensive safety plans and guidelines.
Different workplaces in construction
When we think of construction, we typically think of building sites, machinery, and people in hard hats. But did you know construction work also includes office roles like project management, contract administration, and reception.
When we discuss work health and safety in construction, we need to include everyone under the big umbrella. From wearing earmuffs while using power tools, to having ergonomic seating in an office, there are ways everyone can benefit from a bit of extra knowledge and support.
On-site
On-site construction refers to everything that happens at the place where building work is done. If you’re pouring concrete to make the foundations of a house – you’re on-site! If you’re back in the office doing paperwork – you’re off-site.
On-site, there are lots of things that could cause potential injuries, such as:
- Loud machines
- Loose nails
- Broken glass
- Uneven ground
- Power tools
In these kinds of workplaces, it’s super important to keep your eyes peeled and watch for hazards. Before you commence work, your site supervisor or employer should check that everyone has completed any required safety training.
Off-site
When we talk about off-site workplaces, we mean the places behind the scenes. Estimators, designers, and consultants often work in office-like environments. These kinds of jobs are also referred to as white-collar roles. Even if they’re not on a busy construction site, they still have to watch out for their physical and mental health.
Common health and safety risks you could encounter off-site include:
- Lifting heavy boxes
- Excessively bright lights
- Unsafe environment (exposed wires, leaking roof)
- Poor hygiene
Off-site workers can also experience similar situations to on-site staff, such as being exposed to loud noises or dangerous work equipment. Although their environment is a little different, off-site construction staff still need to undergo health and safety training.
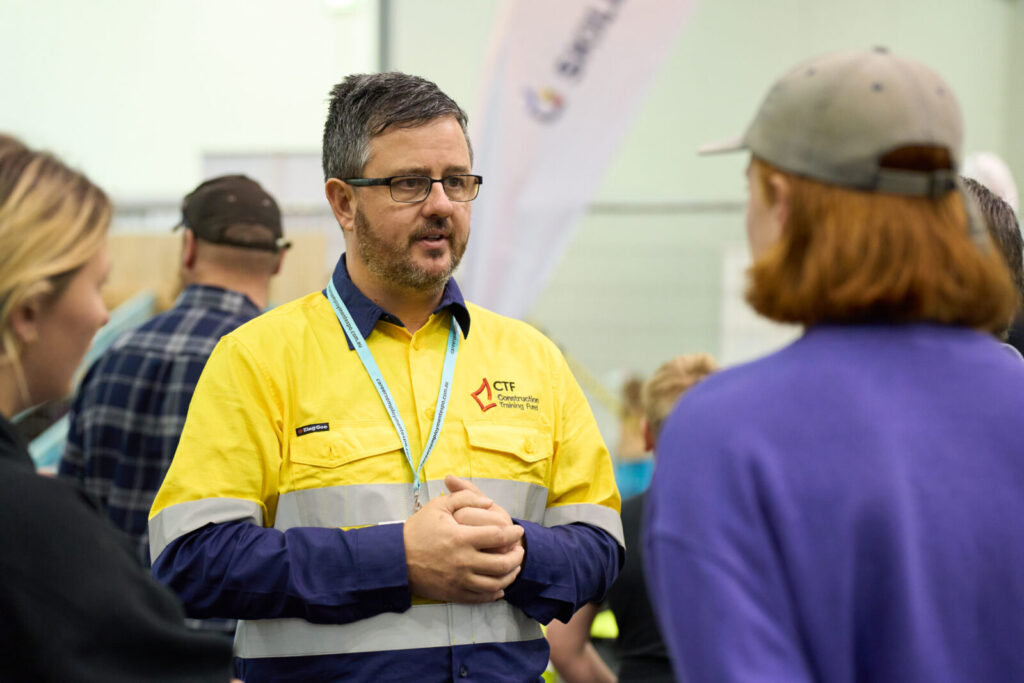
What makes a workplace unsafe?
There are many contributing factors to an unsafe workplace. On or off-site, we all need to stay on our toes and be aware of hazards. Lifting big loads, not wearing the correct safety equipment, and being under stress can all lead to an unhealthy work environment. That’s why we have detailed work health and safety guidelines in place to protect us.
Heavy lifting
Lifting heavy loads, such as boxes or building materials, can actually result in musculoskeletal disorders, or MSD. MSD are illness or injury that directly affects your muscles and joints. Sprains, carpal tunnel syndrome, and back injuries are all examples of MSD.
Attempting to carry large objects without proper training can result in injury to yourself and others. It’s the responsibility of employers, WHS advisors, and employees to teach and learn safe lifting techniques to reduce the risk of injuries. Workplaces can also implement strategies to reduce the amount of heavy lifting staff need to do. This could include placing heavy boxes on trolleys or using lifting machines that can help prevent these risks.
Falls and slips
On construction sites, falls and slips are bound to happen. There’s uneven terrain and lots of equipment, and you’re open to the elements. When a site is exposed to lots of harsh sun, the ground can become dusty and easy to slip on. On the other hand, when it rains, we’ve got mud and puddles to contend with. There are many materials like wood, metal, and concrete to trip over.
In an office setting, there’s also the risk of tripping on computer wires, wet floors, or uneven carpet. Luckily, most workplaces have signage to indicate potential tripping hazards, so we know to avoid them until they’re resolved. However, sometimes we can’t spot the problem right away, so it always pays to be aware of your surroundings.
Lack of PPE
PPE stands for personal protective equipment. These are tools or equipment like hard hats or bright high-visibility clothing that’s designed to minimise our exposure to hazards. Construction sites typically have standard requirements for PPE, and workers won’t be allowed on-site without proper protection. If you don’t wear PPE, or wear the correct sort of PPE, you risk exposing yourself to accidents and injuries.
Unqualified personnel
Unqualified personnel on construction sites can lead to a variety of safety concerns. When you pursue a career in construction, you’ll likely undergo all the necessary training to operate the tools needed for your specific job. However, if you’re required to work with equipment or machinery you’re not familiar with, without having the proper training or inductions, it poses a risk to yourself and those around you. To combat this, employers typically perform background checks or request copies of your training documents and certifications. They should also provide staff with relevant training for any new skills that are incorporated into their workplaces.
Workplace stress
Our work environment has a bigger impact on our mental health than we realise. It’s all well and good to wear safety gear and put up signs, but if you’re working in an unhealthy environment or performing tasks that cause mental stress, that’s a health and safety concern. This kind of hazard is commonly referred to as a psychosocial hazard.
Examples of psychosocial hazards include:
- Poor job support
- Lack of organisation in a workplace
- Bullying
- Workplace conflicts
- Remote or isolated work
In most cases, staff can speak to their employers or company about workplace stress or psychosocial hazards. There are also work unions and organisations like WorkSafe WA that support health and safety in the workplace.
How to stay safe in a construction workplace
Before conducting any construction work, there are a few things to consider. Make sure to read through your contractor or employer’s WHS management plan, wear the right PPE, and understand how to identify and resolve health and safety issues responsibly.
Australia relies on the construction industry, which means the importance of work health and safety is high. Upholding safety standards projects you, your co-workers, and the construction industry.
Wearing correct PPE
Before you start work, make sure you’ve got the right gear. We all need a bit of protection, even for small tasks, just like wearing shoes outside to keep your feet safe. Most workplaces will let you know what kind of protection you need, or it will be outlined in the safety management plan. For example, when operating loud machinery, your workplace may require you to wear earmuffs. This reduces noise pollution and reduces the risk of developing hearing damage.
Other common forms of PPE include:
- Hard hats
- Safety glasses
- Steel cap boots
- Masks
Being aware of surroundings
It seems simple, but you can avoid a serious accident or injury just by looking around. Before performing a task on or off-site, ensure the area is clear of hazards like potholes, unsafe machinery, or fallen objects. Look for discarded nails, technology cables, and tools.
You should also check if there are people around who could be impacted by your work. The last thing you need is someone running in front of you while carrying a big box or operating a forklift.
Clearly display signage
Proper signage is a key element of maintaining a safe work area. Supervisors or managers typically set up signage like electrical hazard signs or wet floor warnings. Signs don’t just indicate immediate issues; they let you know what kind of work is being performed in a certain location. They’re also posted near emergency routes like evacuation pathways and assembly points.
Communicate with employer
If you’re a staff member concerned about your safety, it’s imperative to talk with your employer. They can help you understand best safety practices or provide the correct training and licensing needed to perform certain tasks. It’s especially important to always inform your employer of immediate hazards, such as live wires or broken glass on the floor.
Follow safety guidelines
Workplaces are required to have adequate safety guidelines and procedures. These are available for staff to read. It typically includes a safety management plan that covers policies, training, risk management processes, and injury management. Make sure you have a read-through before starting work.
Often, you’ll need to sign a safe work method statement (SWMS) document verifying you’ve read the safety materials provided.
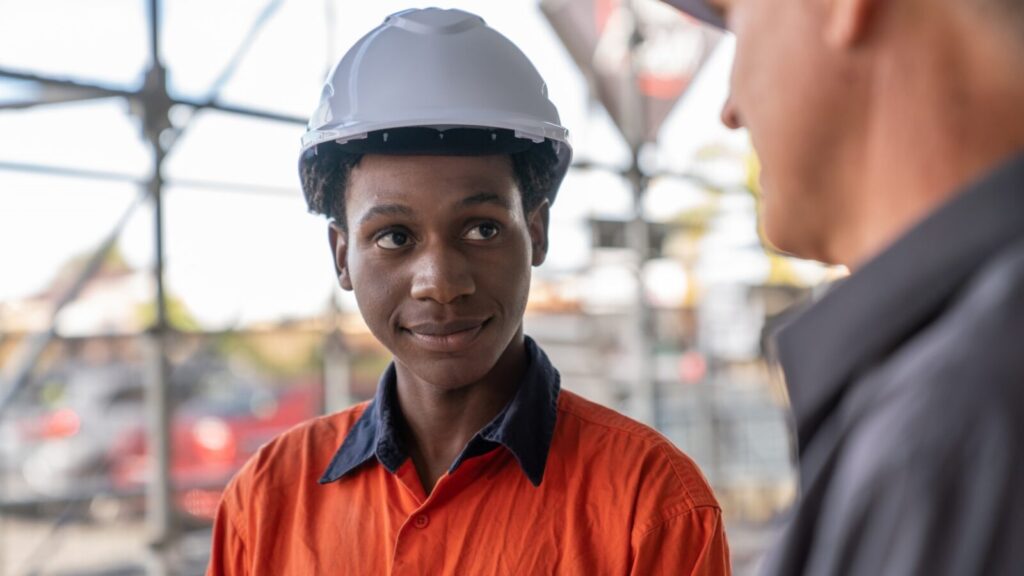
How to improve safety in a construction workplace
The best way to improve safety in a construction workplace is by reading up on best practices and learning WHS skills. When you’re aware of hazards and how to deal with them, you’re making work a safer place for you and all your workmates!
Learn about best practices
Familiarise yourself with WHS procedures. Ask your employer or discuss the protocols and guidelines with a WHS advisor. Understanding best practices for identifying and minimising hazards is an important skill. Safety management plans should be regularly reviewed and updated to ensure ongoing support of safe work.
Take a first aid course
Knowing first aid is a great skill to have. With this kind of training, you can respond to accidents and injuries that result from workplace hazards. Learn how to elevate a sprained ankle or manage an allergic reaction. Some workplaces require first aid training, but for others, it’s optional. If you’re working in construction, you may be able to complete an approved first aid short course with CTF’s support. Our rebate could cover up to 80% of your training costs.
Get familiar with common workplace hazards
Safety gets easier if you know what to look for. By getting familiar with common workplace hazards, you can stay sharp and prevent accidents before they happen. Paying attention to your safety training and researching hazards that occur in your specific workplace are both valuable ways to achieve this.
Workplace health and safety is always a top priority. Did you know CTF is a big fan of upskilling and training in workplace safety? We understand the importance of learning new things or brushing up on old knowledge. That’s why we offer funding and support for approved short courses on work health and safety. If you’re curious about the next step in your construction career, check out the top ten short courses funded by CTF.
Last modified on: